We manage risks to bring impressive experiences.
Uni-Systems Engineering is a single source provider of custom mechanization for iconic structures and attractions that deliver impressive experiences for our customers and the general public. We partner with engineers, architects, and construction managers to mitigate risk and deliver functionally integrated, reliable showpieces. Our team of mechanical, structural, and electrical engineers specializes in providing custom, project-specific solutions to complex and unprecedented engineering challenges.
Single Source
We help mitigate risks that can occur between design and construction. Our team is at your side, from start to finish.
Specialized
Projects are backed by our unmatched technical expertise and broad experience with custom mechanization.
Reliable
As pioneers and market leaders since 1968, we have a reputation of completing innovative world class projects.
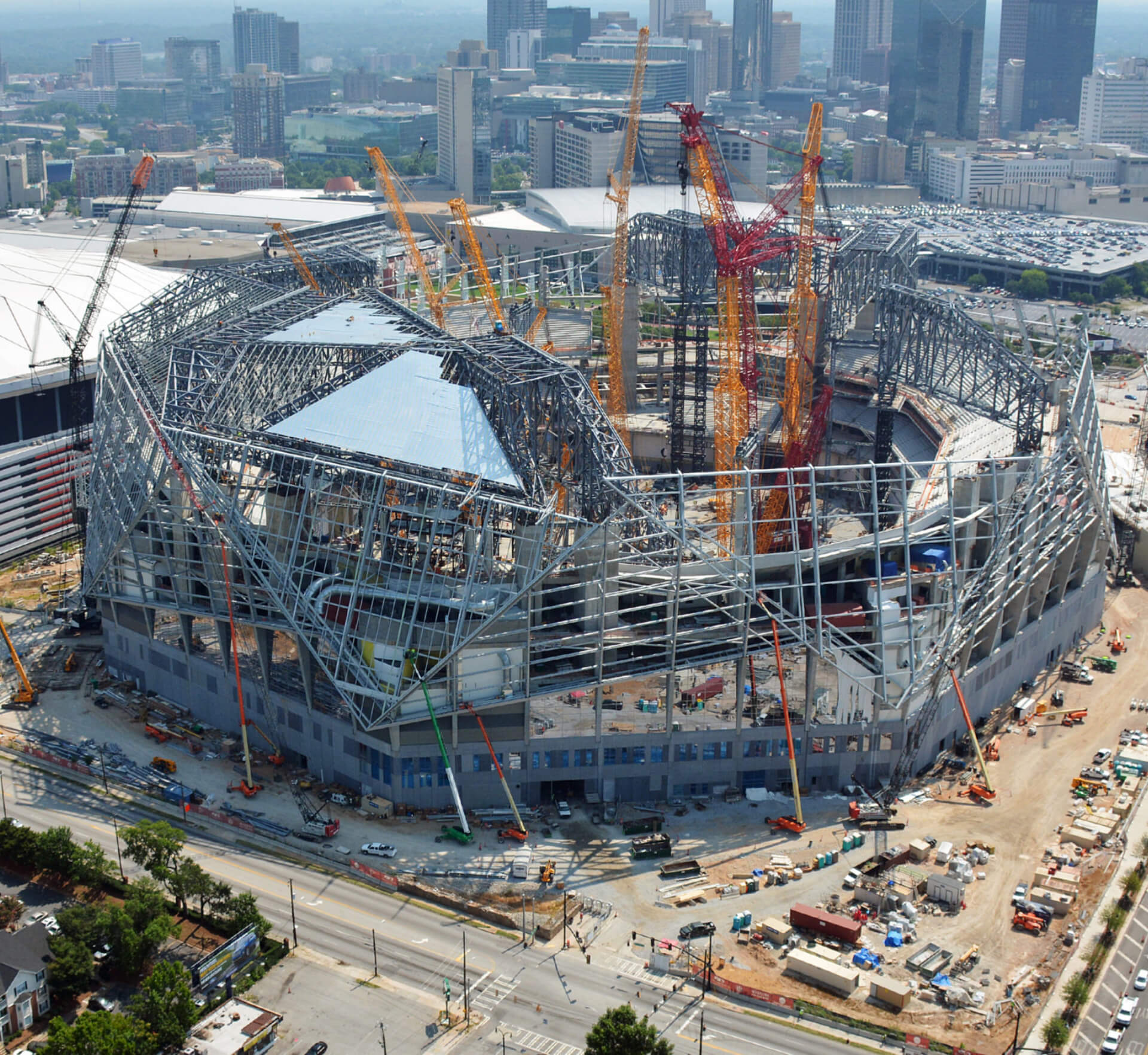
Industries
We provide a variety of services to a variety of industries, with the common thread being the mitigation of risks associated with custom mechanization in reliability-critical, high profile applications.
Featured projects
View All ProjectsWe develop project-specific solutions to complex and unprecedented engineering challenges.
Contact us for a a customized solution for your project.